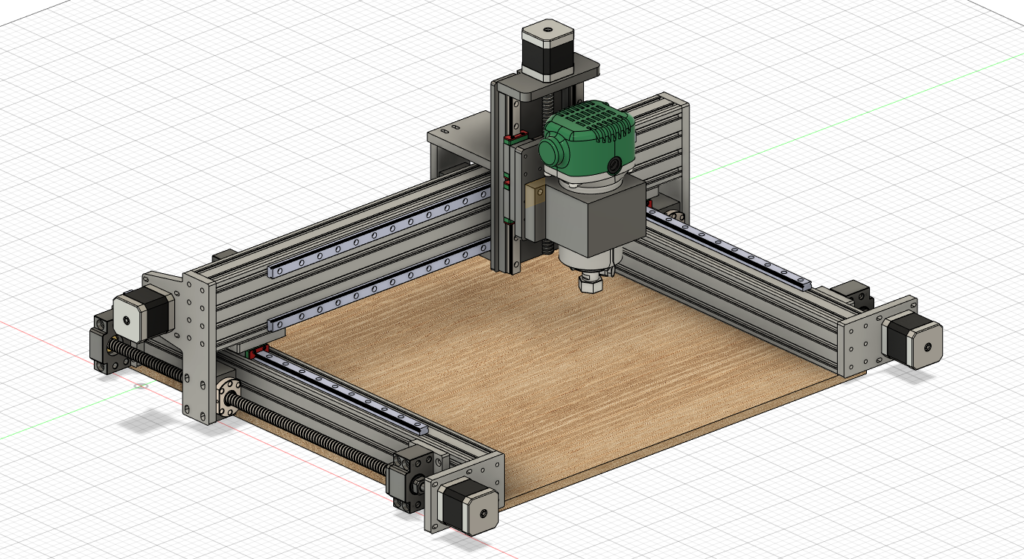
Ya tenemos lo que va a ser la base de este diseño. Después de estar varias semanas dando unas vueltas al diseño, este va tomando su forma final, la cual se convertirá en el proto físico. Vamos a ver algunas cositas.
En esta actualización, os muestro como va a ser la maquina, y sobre este diseño estará generado el BoM que veremos a la semana que viene. Partimos de un modelo base, el cual con el tiempo puede sufrir cambios y mejoras que se nos ocurran a todos. En algún punto hay que trazar la linea de fiscalización de un diseño, pese a que pueda ser mejorado, y eso lo dejaremos para el apartado pertinente de updates. Aun así, al prototipar un diseño, siempre va a sufrir pequeños cambios y ajustes necesarios. El papel lo soporta todo, pero cuando pasamos a la realidad…
En el primer capitulo, ya comente características y elementos principales. Todos los datos de medidas y series elegidas los veremos en el próximo capítulo sobre los números que nos da el diseño 3d. Ahora quiero comentar sobre la maquina en general y posteriormente hablaremos exactamente de que es cada cosa.
El Chasis
Nos encontramos con un chasis que va a ser construido en aluminio. La perfileria, piezas, soporte spindle, son elementos que están construidos con este material. Para el caso de las guías, pues estas son de acero, lo mismo que los husillos. En esencia, esta maquina cuenta con sus principales elementos metálicos. Sabemos que un chasis podrá trabajar con cierta soltura materiales similares a los que esta hecho su chasis. Esto no quiere decir que no podamos mecanizar otros mas duros como por ejemplo acero. Se puede hacer, pero con unas velocidades de avance y espesores muy pequeños, y teniendo en cuenta que estos trabajos han de ser puntuales. Por lo tanto, punto a tener en cuenta si estáis en fase de diseño de vuestra maquina. ¿De que material tengo que fabricar mi chasis? El material ha de ser mínimo el que vayas a trabajar. Podemos saltarnos esta pequeña regla, aumentando de forma muy considerable los espesores de los materiales elegidos, para ganar esa rigidez necesaria que nos va a exigir el material que vamos a mecanizar.
Perfileria de la serie 20 y en configuración 4060 y 4080. Si os acordáis de las imágenes publicadas en el capitulo primero, el perfil del puente era también 4060. Dado que vamos a montar un spindle que pesa un poquito, y el coste entre la 4060 y la 4080 es muy poquito, he creído conveniente cambiarlo y así ganar un poco mas de rigidez para evitar la flexión del puente cuando estemos trabajando en la mitad del puente. También se ha ganado un poquito mas de área sobre la que el soporte del spindle recae cuando esta trabajando. Nos queda un conjunto mas robusto.
Los perfiles que corresponden al eje Y, permanecen en 4060 y nos darán una altura de unos 6 cm como altura útil para el eje Z. De esto ya hablamos en el capitulo 3.
El mártir o zona de trabajo
Una de las claves que posibilitan este diseño, pasan por anclar firmemente nuestro mártir a los perfiles que forman el eje Y. Hemos reducido elementos del chasis y de alguna forma tendremos que reemplazarlos. Si no fijamos nuestro chasis a la mesa, tan pronto como la fresa toque el material, nuestra maquina se nos ira de paseo a donde mas le interese. Al no tener un frame sobre el que apoyar y anclar el mártir, tenemos que unir adecuadamente la superficie que va a hacer de mártir.
Cuando penséis el diseño de una máquina, recordar que la base de trabajo pertenece a la maquina, de una forma u otra, esta zona ha de tener una unión fiable y solida. Es un punto muy importante, porque ya podéis hacer el mejor chasis del mundo, que si vuestra zona de trabajo no es firme, el resultado final va a ser cualquier cosa menos bueno.
Por tanto, nuestra base de trabajo podrá ser de madera o podra ser de aluminio. Si el caso es que sea de madera, podemos montar un tablero de MDF de unos 20-30mm de espesor. Mientras que si es de aluminio, podemos montar una pieza de 15mm de espesor. A estas piezas, podremos o bien hacerle unas ranuras o bien una matriz de agujeros y usar insertos para roscar (en el caso de la madera) o roscar los agujeros en el caso del aluminio. Tratándose de una maquina de iniciación, yo recomendaría montar primero una pieza de madera con una matriz de agujeros y mas adelante, como un posible update de la maquina, cambiar a aluminio.
Sea cual sea vuestra elección, la superficie de esta pieza, lo que sería el área útil, habrá que planearla para dejar alineado correctamente el eje X con respecto a nuestra base de trabajo. Ambos materiales no tienen superficies rectificadas, y aunque pudiéramos meter una pieza de aluminio rectificado, el resto de elementos del chasis, como lo son sus perfiles o piezas de aluminio, tampoco son de precisión. Tendremos una serie de tolerancias, que deberemos corregir mediante el planeo de nuestra área útil. Esto lo volveré a comentar mas adelante, porque es fácil no darse cuenta y olvidarse.
Los husillos
Turno para los husillos, que en nuestro caso van a ser los tipicos SFU1204 C7. Es el tipico husillo a bolas chino con precisión C7. Recordamos que estos husillos tienen un backlash de 0,01 mm. No esta nada mal para su coste. Por si alguien no se ha parado a pensar sobre que relación puede haber entre su nombre y medidas, me paro un momento a comentarlo:
Husillo SFU 1204:
- SFU: Los tres primeros caracteres, para el caso donde tenemos un un husillo con tuerca simple. Si por el contrario, buscamos un husillo con tuerca doble, tendremos que ir a la nomenclatura DFU.
- 1204:
- 12 -> Este valor nos indica el diámetro del husillo en su zona de rosca, no en los extremos, que suele ser menor. Para esta serie, se suelen encontrar en los extremos valores de 10mm de diámetro en las zonas donde van acoplados los soportes (BK/BF) y 8mm para el extremo donde se acopla el motor. Estos parámetros pueden mecanizarse a medida, hay vendedores que ofrecen el servicio de mecanizado custom con los parámetros que el cliente considere oportunos.
- 04 -> Este valor nos indica cuanto nos vamos a desplazar linealmente si damos una vuelta completa al husillo. Medida en mm, así que en nuestro caso el desplazamiento por vuelta será de 4mm. Interesante tenerlo en mente para calcular nuestros pasos por vuelta o milímetro cuando vayamos a configurar la electrónica.
A modo de curiosidad, la anotación de superior. Nuestra máquina esta compuesta por 4 de estos husillos. Tenemos 2 para el eje Y, 1 para el eje X y el que va integrado en el motor del eje Z.
Alguno puede preguntarse, vaya gasto innecesario montar doble husillo en el eje Y, hay cantidad de maquinas con un husillo en el centro. Y la verdad no es otra que, doblamos el coste para el eje Y, pero ganamos una rigidez y precisión en todo el puente que no podríamos obtener con un solo husillo. Sin contar que nuestro chasis no admitiría la configuración de un solo husillo.
Al disponer de dos husillos en el puente, tenemos este perfectamente bloqueado, y por tanto, no se nos moverá cuando estemos en los extremos del eje X. Este fallo es típico en maquinas así, donde los extremos dan peores resultados. No solamente ganas en rigidez del conjunto si no que también puedes evitar tener que montar un motor superior en caso de tener solo un husillo. Los puentes en estas maquinas, cuando sus medidas son grandes, suelen pesar bastante.
Mencionar que hay maquinas que monta cremallera en los ejes Y (o incluso en el X), cuando estos son muy largos. Los husillos también flexan cuando transmiten la fuerza, así que a veces llegas a situaciones donde tienes que meter un husillo de diámetro muy grande. Sobre todo cuando hablamos de medidas >3 metros. Aquí las cremalleras tienen mejor coste. No obstante, las cremalleras se suelen montar en router para madera, donde la precisión no es un parámetro que se busca, aquí cumplen a las mil maravillas. Para esta forma de transmisión del movimiento, también hay calidades, lo mismo que en guías, husillos, etc.
Si hablamos sobre anclaje, ya habéis visto que la maquina cuenta con soportes BK/BF para X e Y. En el caso del eje Z, al ir el husillo integrado en el motor, no nos hace falta un soporte. Pero, si buscáramos mejoras, en este husillo integrado habría que hacer el mecanizado para meter el acople flotante y darle un toque aun mas robusto. En este caso, esta operación resulta costosa y lo que sale mas a cuenta es montar un eje Z con todos sus elementos por separado. En los próximos meses, veremos algún diseño mas de eje Z, donde todos sus elementos estarán de forma individual, y fabricaremos uno.
Los acoples, aunque no estén representados en el 3d, son los que ya hemos visto alguna vez. Acople semiflexibles para absorber la posible desalineación entre husillo y motor. También nos permite extraer el motor de forma rápida, ya que estos acoples no unen ambos extremos de forma rígida.
Respecto al husillo del eje X, en el render esta mas corto de lo que realmente es. Actualmente tiene uno de 500mm pero el que le corresponde es de 550mm. Por eso lo veis mas corto de lo que debería ser, y no alcanza al motor.
Por ultimo sobre los husillos, la tuerca de bolas, que en nuestra máquina es simple, ira unida a su pletina correspondiente mediante un housing de aluminio. Es un elemento que suele tener forma de cubo y nos permite unir de forma rígida y fiable tuerca con su parte móvil correspondiente.
Las guías
Las guías que vamos a montar en esta diseño son las típicas MGN12 con su modelo de patín largo (H). Es la guía que mas nos podemos encontrar en muchas de las maquinas del mundo maker, económica y con una precisión suficiente para el enfoque de nuestra CNC. Por supuesto que hay otros modelos de guías, y también mejores, pero se nos van del objetivo económico. También sería posible montar unas guías MGN15, pero para ello habría que rehacer varias de las piezas de aluminio. Esto quedará como una posible mejora.
Los tres ejes de esta maquina van montados sobre su pareja de guías. Con recorridos de 450mm,500mm y 200mm para el eje Z. El eje X y el Z llevarán 4 patines, mientras que el Y, inicialmente va a llevar 2 (quiero probar inicialmente así y no descarto actualizar a 4. El coste se incrementa en unos 13€ aprox.). Se va buscando dejar una maquina con los costes reducidos, y tocara probar esta configuración.
La totalidad de las guías van soportadas sobre sus correspondientes perfiles o pletina de aluminio. No existe ningún tramo que quede al aire, es decir, que no apoye sobre algo. Esto nos da como resultado un montaje mas robusto. Aunque las guias son bastante rígidas, no dejan de ser elementos pequeño y largos, con lo que es fácil que flexen. Podemos encontrarnos montajes con guías en el aire o apoyadas sobre perfiles de pequeño espesor, lo cual da un resultado pobre en rigidez. Las guías nos aportan precisión, no debemos usarlas para buscar rigidez en el chasis. Para esto ya están los perfiles o cualquier otro elemento destinado a lo que sería propiamente el chasis.
Los patines de estas guías no van precargados, por tanto, cuando las compremos, tendremos que mirar que el patín circula por la guía de forma muy suave. Incluso si ponemos la guía en vertical, el patín prácticamente debería ser capaz de caer y circular por la guía sin tener que acompañarlo o empujarlo. Si nos encontramos que nuestro patín no circula suavemente o incluso apreciamos trompicones, será necesario efectuar una limpieza en profundidad del patín.
Estas guías pueden cambiarse por otras mas largas, si queremos aumentar la longitud del eje Y para vuestros diseños custom. Las encontramos fácil en todas las medidas con incrementos de 50mm, pero las podemos pedir a la medida que queramos si hablamos con el vendedor. Hablaremos en un post exclusivo sobre como escalar el Model A.
Motores
Para los elementos encargados de mover las partes móviles, usaremos los motores Nema17 o Nema23. Las pletinas van a ser compatibles con ambos modelos de motor, por lo que cada usuario podrá montar la opción que mas le interese.
Los Nema17 de mayor par, serán capaces de mover la maquina con soltura, mientras que si se busca una mayor velocidad, los Nema23 nos proporcionaran esta capacidad de forma fiable. La electrónica encargada del control de los motores, dispondrá de unos drivers TMC, los cuales hay varios modelos disponibles, con mayor o menor capacidad para suministrar la corriente necesaria. Sobre la electrónica hablaremos en un capitulo aparte.
Las pletinas de los motores tendrán la posibilidad de realizar un ajuste en uno de sus dos ejes, quedando el ajuste del otro eje en la pletina que va sobre la tuerca de bolas. Hablando de ajuste para alinear todo correctamente y que nos quede un movimiento suave de los elementos que se desplazan.
Terminando...
Y hasta aquí, hemos dado un repaso general a los diferentes elementos que componen chasis y mecánica. Es una maquina sencilla, no es un concepto nuevo, pues hay máquinas muy similares a esta, pero este tipo de diseño que hemos adoptado es bastante económico, pues nos ahorramos todo el frame de la base de trabajo y en tamaño de algunos elementos.
El diseño que os he mostrado hoy, aun es provisional, todavía puede sufrir cambios. Si los hay, los iremos viendo detenidamente. Aun así, me queda acabar alguna pieza con algún detallin, como por ejemplo el acople con patines y pletinas del husillo del eje Z.
En los próximos capitulos, veremos el BoM; He de decir, que finalmente no he podido cumplir completamente el objetivo principal de costes. La cifra actual ronda los 700€, y me habria gustado que fuera mas cercana a 500€, pero también hablamos de una cifra con la maquina completa, electrónica incluida (una SKR 1.4), eso si, no esta contado el mártir. En el capitulo del BoM, lo publicare y a ver si entre todos, podemos reducir costes. Esta difícil bajar sin sacrificar algún elemento, pero nunca se sabe. Puede que alguien tenga un vendedor con precios muy buenos y se acabe mejorando.
También veremos medidas, creo que ira junto con el BoM, veremos lo que me da tiempo a prepara. Y no me olvido de una entrada con posibilidades para la electrónica de control, que apenas hemos comentado nada de este aspecto. Otra entrada será solo para ver como y hasta donde sería recomendable escalar esta maquina, sin perder de vista la rigidez de esta. Posibles mejoras y algunos detalles mas, también tendrán su momento.
Todo esto es lo que llevo en mente de traeros este mes, luego llegamos a vacaciones y un merecido descanso para todos. Igual dejo alguna cosa preparada, pero es probable que se avance poco en este proyecto. Tras las vacaciones, tocara pedir material y ponerse con el prototipo.
Esto es todo por hoy, enviarme vuestros comentarios y sugerencias y nos vemos en el siguiente.
Un Saludo,
Hola me encanta la idea.
Gracias por compartir el diseño y más aún por hacerlo abierto, además de ir explicando cada detalle y los por qué de cada cosa.
Si me permites te propongo un par de ideas, no se si acertadas., pero por hablar de la máquina.
Como tú dices en los carros de Y creo que sería mejor meter 2 patines en cada lado y una escuadra de 90º entre el frontal del perfil y la pletina que soportará esos 2 patines. Piensa que todo el peso del router y carro de Z esta muy por delante del único patín, por lo que este soportaría un par continuo Hacia delante. Con 2 perderías algo de recorrido en Y pero todo el puente estaría mejor soportado y rígido.
El segundo comentario es sobre los perfiles de aluminio. Creo que el perfil 40×80 (serie 40) es algo más barato y con mejores valores de rigidez que el 40×80 de la serie 20, al menos en Motedis. Lo único que la ranura es de 8mm y las guías van a asentar en menos superficie del perfil, pero para los esfuerzos de esa máquina no creo que sea problema o si lo fuese bastaría con meter una pletina de poco espesor entre perfil y guía. Pero vamos yo monte guia de 15 en perfil de esos y no me dió problema alguno.
Y la tercera cosa ya es más sobre gustos, en el carro de Z, ¿no te planteaste poner las guías al revés?, o sea patines fijos en el carro de X y las guías móviles con todo el carro de Z. Por saber tu opinión sobre una forma o la otra.
Saludos y gracias.
Hola Fernando,
Gracias por tu respuesta. Vamos a ver si no me dejo ningún punto de los que has expuesto:
– Creo que llevas razón en lo referente a que con dos patines va a quedar mas robusto el puente. Esta contemplado como mejora y es muy probable que la aplique directamente en el proto, el coste incrementa unos pocos euros. Sobre la escuadra extra que comentas, no sabría decirte. El perfil apoya sobre una pletina de aluminio que a su vez apoya directamente sobre el patín(es), anclado en 6 puntos por cada lado en la cara donde apoya sobre la pletina del patín (independientemente de la pletina del lateral que va a la tuerca). No obstante, comprobare flexiones del puente para ver el punto que comentas. Lo anoto como posible mejora para verificar en el proto. Ahora mismo, el diseño admitiría el segundo patín y se perderían 15mm como mucho.
– Sobre los perfiles, pese a no disponer datos, únicamente el precio, puede que el 8040 de la serie 20 sea ligeramente mejor. Mi razonamiento viene muy cogido con pinzas, me baso en el precio y en que quizás haya mas material en ese perfil. Hay paginas donde tienen la serie pesada del 4080 y esa le daría mil vueltas a la serie 20. No obstante, he elegido la serie 20 porque me permite colocar mas distancia entre patines para el eje X y así el carro del eje Y tiene un poquito mas de área sobre la que apoya y porque me permite tener 2 ranuras en el lateral corto para anclar a la pletina que va sobre los patines. Así que debería quedar mejor así, con la serie 20 en configuración 4080. El punto que comentas sobre la zona de apoyo, es mejor una ranura mas estrecha para apoyar la guía. La guía también la mueves ligeramente para alinear, con lo que si la ranura es muy ancha, puede quedar la guía sin casi apoyo en alguna zona. Si tienes que andar metiendo una pletina para añadir apoyo, también encareces. Tendrías que hacer todos los agujeros y roscas de cada guía, hay un ratito de trabajo ahí metido. Para postre, las caras de estos perfiles no suelen ser muy planas, y ya depende un poco del segmento que te toque del perfil. Si por lo que fuera no quedara lo suficientemente rígido, siempre se le puede meter epoxy granite dentro.
– Sobre el Z, este diseño lleva una pletina muy pequeña como para colocar las guías y patines invertidos. Se quedaría zona de la guía al aire y no tiene sentido. Este diseño que comentas, con las guías invertidas, puede darle un poquito mas de rigidez al conjunto, pero también es mas lioso para alinear. Ya de por si el eje Z cuesta un poquito dejarlo todo bien ajustado, si le añades la dificultad de no poder acceder cómodamente a todos los tornillos, se vuelve aun mas tedioso. No obstante, las guías no deberían usarse para dar rigidez, de eso se encargan las pletinas.
Creo que te he respondido a todo, si hay algún punto que no lo esta, me dices.
Gracias por leerme!
Saludos,