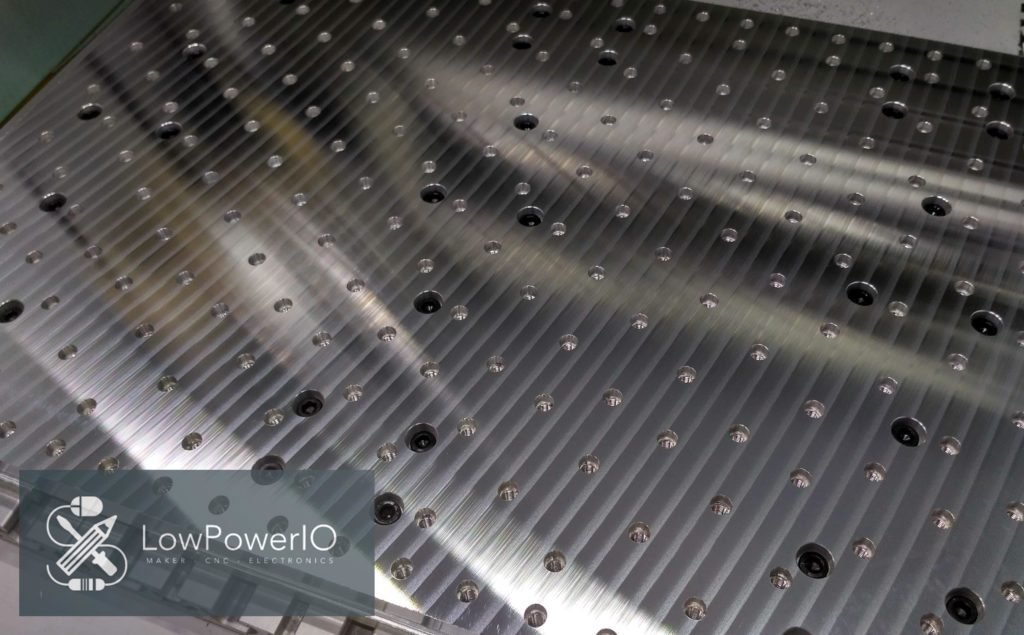
Tan importante como tener una fresadora robusta es tener unos buenos accesorios. En este caso, vamos a ver como podemos hacer nuestro propio fixture plate para CNC.
Sobre el tema de discusión referente a ¿Qué tipo de mesa para la CNC es mejor? Hay infinitas respuestas. Y es que depende de cada trabajo que vayamos a hacer, depende de la construcción de nuestra fresadora diy cnc, y un interminable etc etc. Por tanto, una solución simple es hacer utillaje conforme descubramos que lo vamos a necesitar o encontremos situaciones donde necesitamos resolverlas con elementos extra, como por ejemplo mediante un fixture plate para la CNC que cubra la mayor parte posible de mi mesa en la fresadora diy cnc CNCDesktop 500, de diseño propio.
Cuando montamos nuestros router CNC, lo mas versátil es montarnos una mesa que nos permita trabajar con comodidad o nos de la mayor flexibilidad posible. Los diseños que mejor encajan aquí es meter una mesa de ranuras o una mesa con una matriz de dimensiones conocidas de agujeros. También podemos meter en esta corta lista una mesa de madera para clavar el material. Esto es muy frecuente verlo en los router CNC que trabajan madera.
Cuanta mayor sea la flexibilidad que nos permita la mesa, mejor podremos adaptarnos a las necesidades de los trabajos que vayamos a realizar. Y ojo cuidado, SIEMPRE va a existir ese trabajo que necesite de elementos extra para realizarlo. Mas aun, con nuestras maquinas CNC caseras.
¿Qué problemas tiene una mesa ranurada o de perfil?
Problemas problemas ninguno, a no ser que la hagas con piezas de perfil tipo 16016 o similares. Que son perfiles de poco espesor pero anchos con ranuras. Y es que estos perfiles baratos, y probablemente ocurra con todos, no son perfectos, ni de precisión. En la extrusión no existe esa precisión que puedes necesitar para construir una maquina, y necesites rectificar ciertas partes.
En el caso del perfil de Motedis (en mi caso el 16016), este tiene un error en los laterales bastante grande, y que no es plano. El maldito perfil es mas alto en los laterales que en el centro, y esto es toda una señora putada cuando tenemos que trabajar piezas que ocupan mas de un bloque.
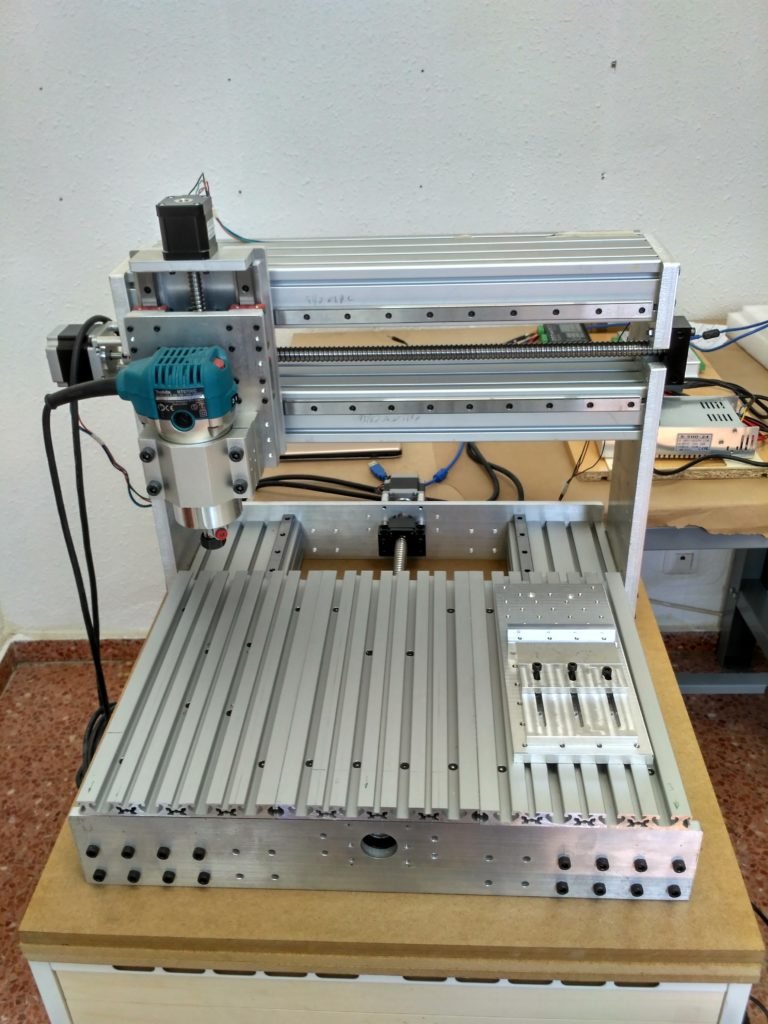
Mi mesa de la CNCDesktop 500 esta formada por 3 piezas del 16016. Así que tengo 2 líneas (o mas bien dos zonas) que son como dos montañitas.
Si os fijáis en al foto, podéis apreciar que la mesa de perfil, son 3 piezas.
Es una mesa cómoda de usar, todo hay que decirlo, pero también barata. Ya que si buscara una pieza de perfil en bloque, de ese tamaño, la broma puede costar entre 600 y 1000€. No son nada baratas esas mesas, pero por contra, no tienen este problemilla de que no es plana.
Una solución es hacer un planeado de la mesa (una vez montada, no antes), pero al ser la mesa mas grande que el área útil de la CNC, va a quedar feo, poco útil, y no me gusta.
La solución para por fabricar utillaje, que en el caso de querer usar toda la superficie, pues tendremos que hacer un fixture como el que vamos a ver hoy, pero que si necesitamos anclar piezas que nos entran en uno de los tres bloques, podemos hacer fixture plate mas pequeñitos, como el fixture plate prototipo que vimos en su día. Y que me sirvió como experimento y base para el que vamos a ver hoy.
Para operar en los trabajos donde se necesita la precisión de la altura, ya sea porque tenemos que mecanizar laterales que su ángulo en 90º es crítico o los mecanizados en espesor también lo sean, operaciones en general donde no mecanizamos el espesor completo del material, etc. Vamos a necesitar fabricar una plancha, que puede ser de 1 tercio de la mesa, de 2 tercios o completa, según lo que necesitemos.
Estas planchas de utillaje, las vamos a llamar fixture plate, porque además de permitirnos colocar el stock con precisión en altura, podemos añadir todos los puntos de anclaje que queramos, o incluso hacer fixture específicos para formas concretas de las piezas. Si necesitamos voltear o trabajar en serie, también tendremos nuestros propios fixture plate. Es tan importante como las fresas. El utillaje nos soluciona la vida ante problemas de anclaje.
Como es lógico, puede haber infinitos diseños, pero no hay uno que puedas decir, este es el mejor, no! Cada uno tiene un propósito concreto, si que podemos decir que si has de hacer algo general que sea flexible, vuelvas a recurrir a lo que he comentado mas arriba, o bien haces una matriz de agujeros o bien haces ranuras.
Ventajas de hacer tu propio fixture plate
Comercialmente existen un montón de modelos, hay varias empresas que comercializan estos productos. Y hoy en día todos cuentan con archivos 3d para cargar en nuestros programas favoritos y así poder cargar nuestro diseño sobre el fixture, o hacer otro fixture para anclar, pero dispondremos de los puntos de anclaje y podremos trabajar con mas precisión y repetitividad, que es de lo que se trata.
La principal ventaja de hacer tus propios fixture plate para CNC es que lo puedes hacer como tu quieras! No hay casi reglas a seguir, la mas importante es la de que tiene que ser robusto, así que no escatimes en espesor, y trabaja con mínimo 10mm. Si tu CNC tiene fuerza, que sean 15 o mejor aun 20mm de espesor.
El diseño que pueda servirme a mi, a ti puede no valerte de nada! Que no te de pereza en sentarte a pensar como tiene que ser el tuyo. Si tus trabajos son piezas pequeñas, es mejor que hagas fixtures pequeños, antes que unos grandes.
¿Mesa ranurada o matriz de puntos roscados?
Antes de que se me olvide, por si hay dudas, que es mejor.. una mesa ranurada o de perfil, una mesa con matriz de agujeros o una mesa con un mártir de madera y clavamos donde mejor nos venga? Nuevamente, depende de vuestros trabajos. Así que os hablo desde mis experiencias y necesidades. Yo parto de una mesa de perfil, con sus carencias y el fixture que me he hecho nuevo es con matriz de puntos, para poder usarlos como referencias para posicionar material y otros utillajes que necesite hacer en el futuro. Con el diseño, se pueden hacer futuras piezas pensando en como vana ser ancladas.
No hay una solución clara frente a las demás. Puede que las ranuras den mas flexibilidad para anclar, pero por contra, pierdes toda la precisión en posicionamiento, porque no tienes referencias (a no ser que hagas el grabado de líneas en el perfil). Si que he de decir que es como, y frente a mi mesa de matriz que tenia en mi anterior CNC…mmm difícil decisión. Pero voy a inclinar la balanza al lado de las ranuras, ya que los puntos siempre hay momentos donde justo no tienes uno para atornillar una grapa o lo que sea. Damos mas flexibilidad a las ranuras, no se lo podemos negar. Diría que todas las CNC o fresadoras de columna o centros de mecanizado, son mesas de ranuras. Y muchos fixture son mesas de matriz de puntos que podemos acoplar sin problema.
Si tu trabajo es la madera, el tener el martir de madera para anclar ahí donde toque es buena solución, pero combinar matriz de puntos con ranuras t-slot y laminas de madera, es un combo que cada vez se ve mas. Casi tienes las ventajas de las tres soluciones.
Si tu trabajo es aluminio o metales en su mayoría, mesa de metal y ranuras o matriz de puntos. Recordemos que la madera se mueve y se aplasta fácil. Si buscamos precisó, no podemos tener elementos blandos sobre los que apoyarnos.
La verdad es que este tema daría para escribir y mucho, y de vez en cuando voy haciendo alguna entrada sobre estas cosas. No os perdáis las novedades del blog! Ah! y compartirlo por ahí para que llegue a mas gente, a ver si animamos al personal a que se adentre en estos mundillos!
Consideraciones previas al diseño
Vamos por faena, que me lio a hablar de cosas y nos pegamos hasta mañana en un post muy largo que luego no se lee nadie. Mmmmm… puntos de partida antes de ponernos a diseñar:
- Pensar. Y no, no es una broma, sentaros varios ratos con vuestra libreta a hacer unas rayas con el boli y luego fusionarlas. Pero sobre todo, pensar un poco.
- Dejo de lado todo lo que sea comprar el fixture comercial.
- Si lo vamos a hacer nosotros, recordar que debemos llegar a toda la superficie posible con nuestros medios. A ver si nos vamos a poner a hacer un fixture tan grande que luego no lo vamos a poder mecanizar.
- Al menos hay que refrentar 2 laterales, que usaremos como referencia para poder volver a colocar con precisión el Fixture. Dejo para otra entrada ideas para volver a recolocar, que esto se va de madre. Pero tener 2 zonas que vamos a repasar con la fresa en su totalidad (si es posible). Serán nuestros puntos de referencia.
- La pletina que haga de fixture no puede ser desmotada hasta terminar el proceso, sobre todo si no hemos hecho el refrentado de algún lateral para poderlo usar como referencia.
- Piensa que tipo de matriz de puntos te va a ser mas útil. Luego puedes hacer mas fixture en pequeño con esa misma matriz. Piensa que el utillaje que diseñes para ese fixture, podrás reutilizarlo en otras situaciones.
- Añade a los agujeros un parte inicial sin roscar para meter pasadores, o pequeños cilindros que entren con cierto ajuste para usarlos como tope o para posicionar con precisión futuros elementos extra.
- El espesor, mínimo 15mm, sobre todo en tamaños grandes, como puede ser el caso que vemos hoy.
- Ten en cuenta donde va a ir apoyado, si es una mesa formada por varios perfiles, posiblemente tengas que hacer ciertas piezas y planearlas antes para nivelar correctamente la superficie.
- Evita tener que planear la superficie del fixture, por eso, mi recomendación es el punto anterior y el material para el fixture que sea ya rectificado de fabrica. Creedme que merece la pena pagar ese pequeño extra de mas. Olvidaros de rectificarlo vosotros (a no ser que tengáis medios adecuados y una alta precisión).
- Lo suyo seria usar material mas duro del que inicialmente vas a anclar en el fixture. Esto ya es mas complejo de conseguirlo.
- Recuerda anclar la piezas que vas a planear previamente con un par de apriete conocido, para luego usar el mismo par en todos los tornillos de anclaje del fixture tanto a esas piezas que nivelaran la superficie, como las que van directamente a la mesa de perfil. De esta forma hilamos fino. Es mas importante de lo que pensáis este pequeño paso. Hace poco escribí una entrada sobre destornilladores y llaves dinamométricas. Échale un vistazo!
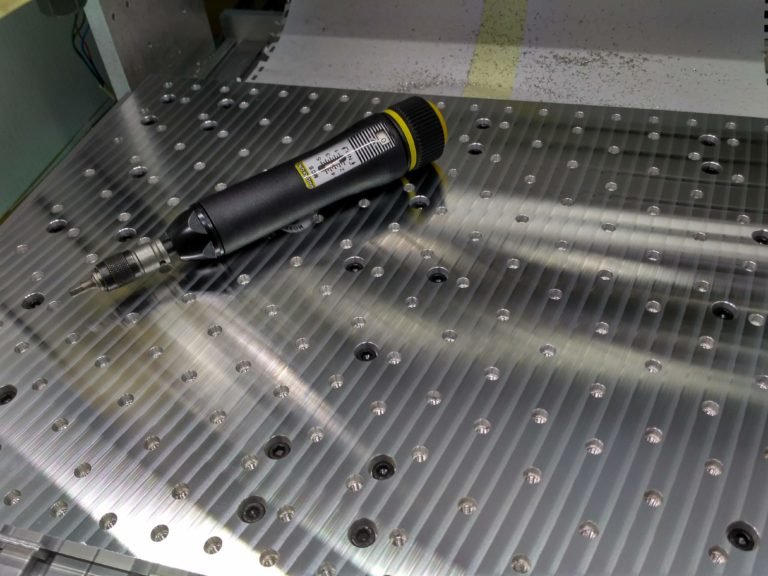
Yo compre el de Proxxon, con rango de 1 a 5Nm, que va perfecto para los tornillos que uso. Cuidado con pasarse con los pares de apriete, porque si el tornillo o la llave no es buena, los pasaremos y luego es una faenada para sacarlos.
Lo idea sería poder usar tornillos torx o tornillos allen y llaves de buena calidad.
Todos los tornillos negros que veis en la foto, están con un par de apriete de 3,2Nm.
Al quitar y volver a recolocar el fixture, siempre se apretaran con ese mismo par. Así conseguimos hilar aun mas fino, y seguir logrando esas centésimas o incluso alguna décima en nuestros trabajos.
El diseño del fixture plate
Para el diseño, yo he usado Fusion360, que aunque la han liado cosa buena con las licencias, no deja de ser un buen soft y tienes la parte CAD & CAM en un mismo programa, que se agradece.
Me baje el 3d de los perfiles míos y monte la parrilla como veis en la imagen de mas abajo. Tras esto, puse 3 piezas de aluminio de 10mm, que creo se pueden apreciar bien en la imagen. Son piezas rectificadas de fabrica y os explico porque:
Aunque una cara va a ser planeada para dejar la superficie correctamente nivelada, si que me interesa que este todo bien plano y con las caras paralelas. En este caso habría dado igual que fuera aluminio normal, pero el proceso de planeado se tendría que haber realizado por las dos caras en las 3 piezas. Al final, esto se traduce en tiempo de maquina, y señores, el tiempo también es dinero.
El fixture en si, es una plancha rectificada a la que no realizaremos ningún proceso de planeado. Así que esta misma nos sirve para colocarla en otras maquinas. Matriz con 200 agujeros para M5 y una pequeña zona inicial de 5mm para insertar un pasador de matriceria de diámetro 6mm.
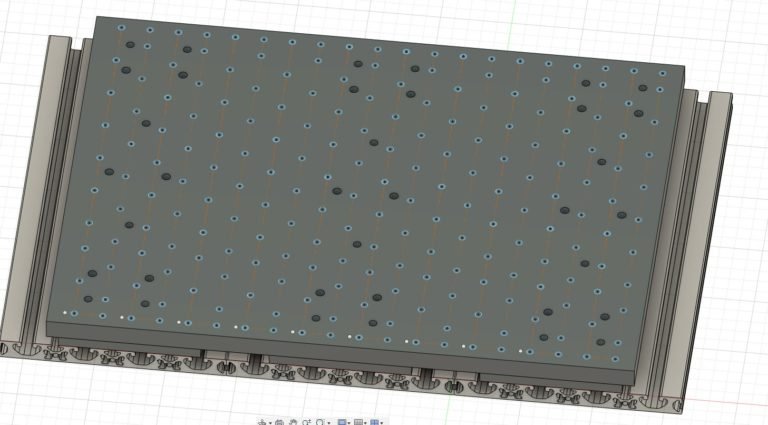
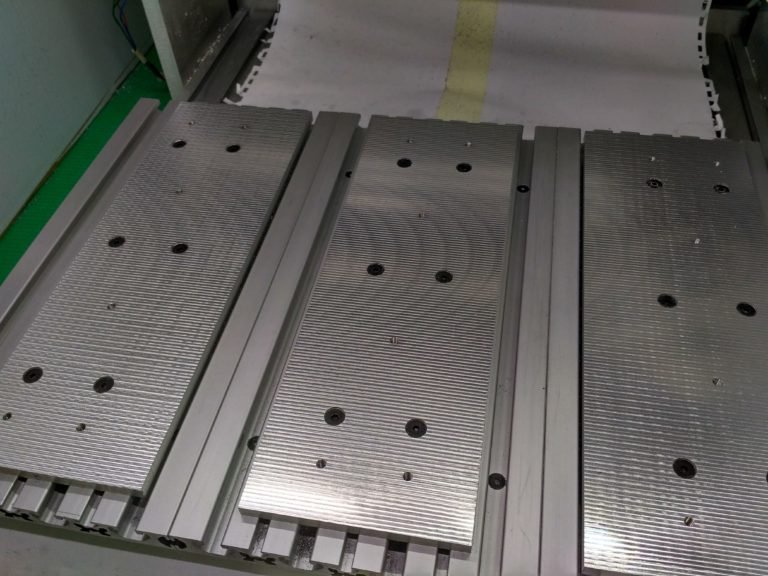
En la imagen de la derecha, se ven las tres piezas colocadas y planeadas, con un “stepover” de 1mm y una fresa de 4mm. Paso fino para que quede realmente bien. Y dos pasadas. Solo es cuestion de quitar 2-3 decimas.
Recordar que estas placas se aprietan a la base de perfil con par conocido. En mi caso fueron 3,2Nm, que ya estaban cerca del limite de los tornillos avellanados. Los 3,5Nm los habrían aguantado pero en algún caso ya observe una deformación considerable.
Con la superficie de las 3 placas lista, se colocará encima el fixture para ser mecanizado.
La fabricación del fixture plate XXL
Me he adelantado con alguna foto y explicación en el paso anterior, pero bueno, no pasa nada. Para la fabricación del fixture plate para CNC, el proceso queda dividido en 2 partes. Por un lado tenemos una fase sencilla de preparación de los soportes donde ira apoyado el fixture en si. Proceso facil, simplemente limpiar los laterales de las tres placas, marcar centros de los agujeros en cada una, realizar las operaciones, roscar los correspondientes y volver a meter en la CNC. Esta vez ya con su posición, pues ahora procedemos a planear.
En esta fase de planeado, estas placas han de ser ya atornilladas con par conocido, que en mi caso es 3,2Nm (el mismo valor que usare posteriormente para todo). Las placas ya no se van a mover en todo el proceso. El fixture lo colocaremos encima y usaremos las grapas para dejarlo anclado.
Para planear, primero hice una pasada en una dirección y luego una final mas fina en la otra. Recordar que los avellanados para poner los tornillos que van a fijar estas pletinas, tienen que dejar la cabeza de esos tornillos por debajo de las pasadas de planear. Luego ya no volveremos a usar mas esos tornillos, ya que usaremos tornillo de cabeza normal.
Pasamos al fixture plate
Vamos con la pieza principal, las fotos de abajo ya son las propias. Bien, plancha de 410x300mm y 15mm de espesor de aluminio rectificado 5083. Tendría que haber sido 7075, pero no esta el bolsillo para gastar mucho.
Le quito una de las dos laminas protectoras, la que va a ir en contacto con las pletinas que hemos preparado antes. Al ser rectificado, sus caras son paralelas y no tenemos que andar planeando de nuevo. Es la ventaja. El aluminio normal no es completamente liso y podemos encontrar diferencias de altura de varias decimas.
Para colocarlo en la CNC, lo grapo en 4 puntos, de los cuales, tendré que ir moviendo uno a uno en el proceso de mecanizado de los agujeros que van en la parte mas cercana a cada lateral. No es problema, solo un coñazo, pero bueno.
Lo primero de todo, preparar el plano de referencia. Aunque no tengo foto, antes he preparado unos topes, que he rectificado fresando el canto para que queden perfectamente alineados. Sobre ellos he apoyado la pletina grande y luego amarrado con las grapillas. Retiro esos topes y freso el lado mas largo en su espesor, para dejar una referencia fiable y rectificada. Lo mismo con el lateral opuesto. Decir que las fresas estas chinas de 3 labios dejan un acabado casi a espejo muy bueno. Con esto listo, pasamos a mecanizar la matriz de agujeros.
Como esta pieza es un poco mas grande que mi área útil, el cero pieza no va justo en el borde del material. Mi maquina tiene 405mm de recorrido útil y la plancha hace 415mm. Tener estos detalles en cuenta para posicionar el material lo mas en medio posible. Y tener esto en cuenta también cuando definamos el origen en el CAM.
Mi cero pieza va a estar en el primer agujero de la matriz, y esa va a ser mi referencia para toda ella.
Así que manos a la obra. Como mi PC no es muy potente, solo pude modelar en 3d 4 filas de agujeros. En el sketch si que tengo toda la matriz, pero en el 3d, solo 4 filas. Cuando iba por la mitad, ya el programa iba fatal y en algún momento hasta se quedaba pillado. Pero bueno, no pasa nada porque todo era exactamente igual.
Fui ejecutando el mismo codigo que me mecanizaba dos filas de agujeros. un detalle, antes de lanzarme a mecanizar todo, hay que hacer el ajuste final del diámetro de los agujeros sobre los que van a ir los pasadores de matriceria. Ese ajuste de la décima, es el que hay que hacer en varias pruebas, variando el valor 0,02mm hasta que tenemos un mecanizado donde el pin entra pero sin juego.
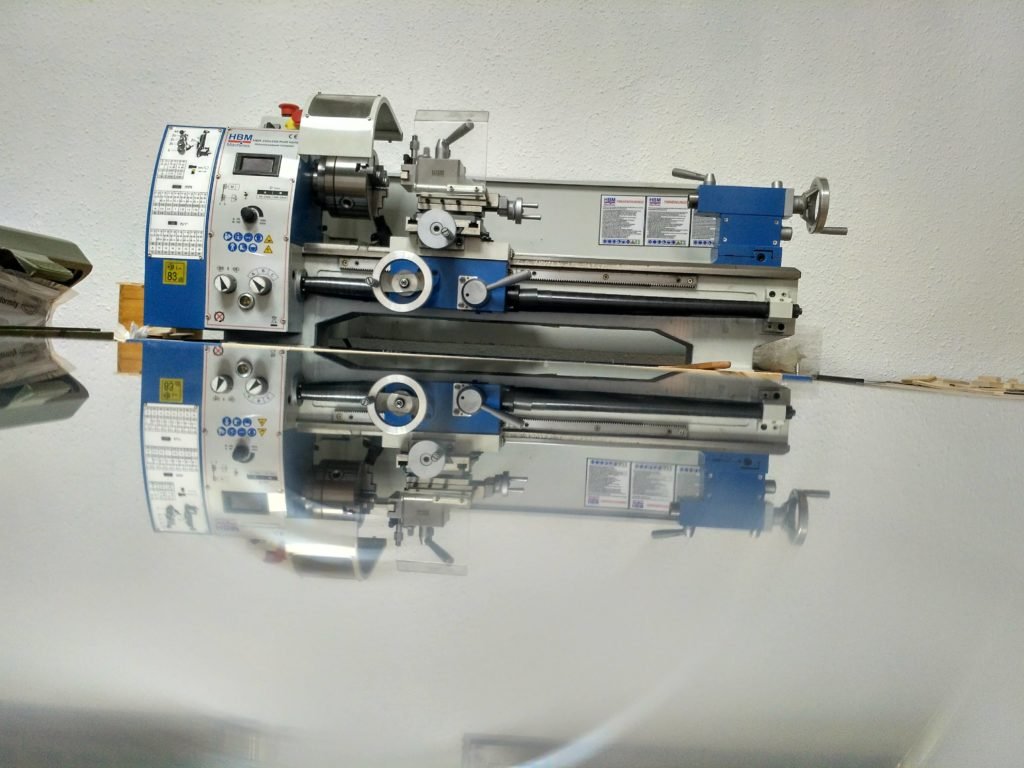
Hay que decir que el aluminio rectificado es muy chulo y da hasta lastima tocarlo. El acabado es casi a espejo y tiene un “veteado” muy chulo jejeje.
Haciendo un poco el gamba, queda muy bien el reflejo del torno.
Ahora empezaremos a hacer cosillas con el, y darle vida a la sección del torno que tengo.
Pero no será como el torno impreso en 3d, usaremos un torno algo mas robusto. Estad atentos, que hay muchas cosillas interesantes.
Nota: Si alguien quiere saber que torno es; Esta comprado en Tecnomaquinas.
En las siguientes imágenes, se ve un poquito el proceso de mecanizado de los agujeros de anclaje con su avellanado. Despacito porque es fresa de 3mm y la viruta del fondo no evacua bien. Estrategia “bore” para el agujero mas pequeño, que hace una bajada centrada en espiral. Aquí vendría genial poder meter asistente de aire para sacar fuera las virutas, que quedan muy trituradas y casi polvillo. Al final lo que hacemos es cortar la viruta una y otra vez. Esto no interesa.
Después de esto viene el proceso de todos los agujeros pequeños. Hechos en bloques de dos filas por cada ejecución del gcode. A destacar aquí que debemos ir modificando nuestro origen de trabajo para el eje X. Como mis filas están todas separadas a la misma distancia, no hay problema.
Os dejo después de estas imágenes un pequeño video de unos segundos.
Tras hacer toda la superficie, hice a mano muy rápidamente un pequeño proceso de avellanado, un par de vueltas sin apretar, que prácticamente no haría ni falta, es ya mas tema personal de que me gusta repasar todos los agujeros.
Pues ya estaría casi terminado. Ahora toca sacar de la CNC, limpiar todo bien, hacer las roscas de los agujeros y proceder a montar el fixture plate para CNC.
Montaje final del fixture plate
Llegamos al final, veis que en pasos esto es realmente sencillo, lo único que lleva su tiempo porque son un montón de agujeros. El tema es que es un fixture plate para CNC que abarca casi toda la mesa y con una matriz de un par de cientos de agujeros.
En este momento ya, procedemos al montaje. Sin apretar los tornillos, montamos las 3 bases, y colocamos todo sin apretar ningún tornillo. Cuando este posicionado en la CNC, se aprietan primero los tornillos que anclan el fixture a las 3 bases. Posteriormente repetiremos el proceso con los que van con los T-Nut, que son los que fijan el fixture plate a la CNC.
No quitéis el pastico protector hasta que no este todo colocado, así evitamos que pueda dañarse durante estas operaciones.
Al apretar todos, y cuando digo todos es todos, los tornillos, se ha de hacer con el par de apriete que fijamos al principio. En mi caso 3,2Nm. Si quitamos el fixture plate de la CNC, y lo queremos volver a colocar posteriormente, deberemos usar este mismo par de apriete. Recordar que para eso usamos el destornillador dinamométrico.
Os dejo un par de videos cortitos mas y unas fotos finales de como ha quedado instalado el fixture plate para CNC.
Y hasta aquí este proyecto del fixture plate para CNC, que se me alargo un poquito en la ejecución, pero ya podemos casi cerrar. Solo me queda hacer unos topes adecuados para posicionarlo de forma relativamente precisa sin andar con el reloj. Para los casos donde no necesitemos colocarlo a la centésima. Esto lo dejamos para otra entrada, porque a saber cuantos habéis llegado hasta estas líneas.
Dejarme en los comentarios vuestras opiniones, sugerencias, etc. Me interesan! Hacer este tipo de entradas lleva bastante tiempo.
Por mi parte esto es todo, nos vemos en la siguiente.
Saludos.
Pd: Si alguien esta interesado en que le fabrique un fixture plate para CNC, puede ponerse en contacto conmigo, arriba a la derecha tiene la opción.
Entradas relacionadas
Entradas mas recientes
Reduce el proceso de lijado con este sencillo truco
En esta entrada os voy a contar una pruebecilla que he realizado esta semana, y no se trata de otra cosa que un método con
Como cambiar los engranajes cónicos al torno de metal
Nuestros pequeños tornos para hobby también necesitan de mantenimientos mas profundos, en este caso vamos a ver como cambiar los engranajes cónicos al torno de
Como cortar vinilo con laser
Voy a tratar de dejaros una guía sobre como cortar vinilo con laser de diodo o laser de CO2. Prestad atención al aviso, pues este